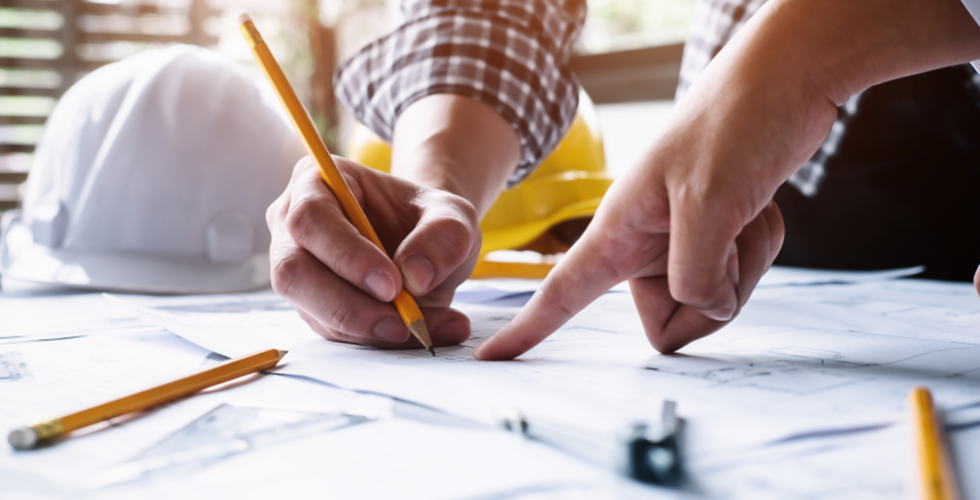
Optimizing Conveyor Design for Efficient Material Handling
In today’s fast-paced manufacturing world, every second counts. Conveyor systems play a vital role in keeping production lines running smoothly, but what truly makes a conveyor system efficient? How do you ensure your conveyor is designed to handle the specific needs of your production process, whether it’s moving heavy automotive parts or delicate electronics? And perhaps most importantly, how can a well-designed conveyor impact not only productivity but also your bottom line?
We know the best for you
Conveyor design isn’t a one-size-fits-all approach. Each system requires careful planning to ensure it integrates seamlessly into existing workflows, handling materials efficiently and reliably. Below, we’ll explore some key types of conveyor systems and critical considerations for designing a conveyor that meets your unique operational needs.
Types of Conveyor Systems and Their Uses
Belt Conveyors: The most common conveyor type, belt conveyors are ideal for transporting lightweight and small items, like packaged goods or assembly components. They’re often used in industries such as food processing, packaging, and retail distribution, where smooth movement is key to preventing product damage.
Roller Conveyors: Available in both powered and gravity versions, roller conveyors are effective for handling heavy and bulky items. This system is ideal in automotive and warehouse applications where larger items need to be transported over long distances without direct power at every point.
Chain Conveyors: Chain conveyors are extremely durable and are ideal for moving heavy or abrasive items, often used in environments such as automotive assembly, metal processing, and pallet handling. These systems can transport items at various elevations, making them versatile for complex layouts.
Key Considerations for Effective Conveyor Design
-
Material Needs
Different items require tailored conveyor materials. For example, fragile items benefit from smooth surfaces, while heavy-duty materials are ideal for bulky loads. -
Speed and Load Capacity
Ensuring the conveyor’s speed and capacity match production needs helps prevent breakdowns and maintain smooth workflow. -
Space Optimization
Compact or vertical conveyors maximize limited space, while large facilities benefit from interconnected conveyor networks. -
Energy Efficiency
Features like low-friction materials and energy-smart controls reduce operational costs and environmental impact. -
Safety and Ergonomics
Guardrails, sensors, and ergonomic heights enhance worker safety and streamline handling tasks.

Conclusion
For manufacturers looking to streamline operations and reduce costs, the right conveyor design can be transformative. At Synergic Hallmark, we understand that every industry and facility has unique requirements. Our team of experts is dedicated to creating custom conveyor systems that not only meet but exceed operational demands—maximizing efficiency, safety, and reliability. Whether you need a new system built from scratch or an upgrade to your existing setup, we’re here to support every step of the way.